Navigating Quality Assurance - The Seven Principles of the ISO 9001 Standard
- About Us
-
Businesses
-
Main Menu
- Businesses
- Our Businesses Overview
-
Textile
-
Businesses
- Textile
- Overview
- Markets
- Brands
- Expertise
- Media
- Contact Us
- Chemical
- Flooring
-
Performance Solutions by Milliken
-
Businesses
- Performance Solutions by Milliken
- Overview
- Consulting Services
- Education and Events
- Resources
- Virtual Tour
- Contact Us
- Products
-
Industries
-
Main Menu
- Industries
- Industries Overview
- Agriculture
- Apparel
- Automotive and Transportation
- Building, Construction, and Infrastructure
- Coatings, Paints, and Inks
- Commercial
- Consumer Goods
- Education
- Energy and Utilities
- Government and Defense
- Healthcare and Life Sciences
- Hospitality
- Manufacturing
- Packaging and Print
- Residential
- Sustainability
- Careers

Navigating Quality Assurance: The Seven Principles of the ISO 9001 Standard
In textile manufacturing, adherence to globally recognized benchmarks is a key way to communicate quality of work and commitment to safety. But with dozens of certifications available to manufacturers, one stands out from the rest—the International Organization for Standardization (ISO) 9001.
Widely considered a gold standard in quality management systems, and seen in 2.1 million companies across 170 countries around the world, manufacturers who have obtained this certification assure consistent, high-quality products and services. Implementing the seven principles of ISO 9001 can be a game-changer in ensuring dependable quality and reliability throughout the supply chain.
Read on for a brief overview of the seven principles that make up the ISO 9001 certification.
The Seven Principles
.jpg)
1. Customer Focus
At the heart of ISO 9001 lies an unwavering commitment to customer satisfaction—including listening to customer feedback, understanding their expectations and working collaboratively to address their needs. In textile manufacturing, this also includes ensuring raw materials, components and the final product meet regulatory standards.
2. Leadership
Strong leadership is the cornerstone of any successful quality management system—and arguably, any company. Organizations with strong leadership set clear objectives, provide associates with resources, and empower team members in order to hit their goals. Great leadership can drive continuous improvement initiatives that enhance efficiency and mitigate risks across the manufacturing process.
3. Engagement of People
In the dynamic landscape of textile manufacturing, the involvement and empowerment of personnel at every level is crucial. This includes fostering open communication channels with suppliers, encouraging collaboration and feedback between team members to identify opportunities for improvement and creating a problem-solving culture. One more cornerstone of this principle is investing in training and development programs, to ensure associates possess the skills and knowledge necessary to uphold quality standards effectively.
4. Process Approach
The idea that resources and activities should be seen as linked processes rather than siloed departments or individual responsibilities is a critical component of this principle. In a manufacturing environment, this is most often seen on the plant floor. A systemic approach, where each function knows it’s role in the overall process, makes room for consistency and dependability.
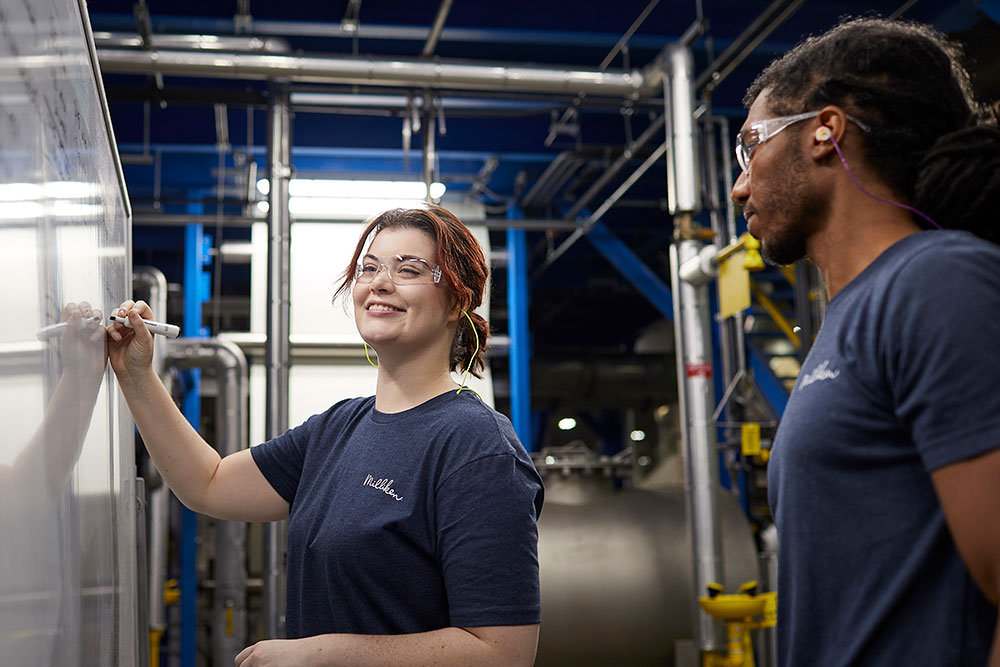
5. Improvement
This principle encourages embracing a proactive stance towards identifying areas for enhancement throughout the supply chain. This could involve conducting regular supplier audits, implementing corrective actions, and leveraging data analytics to drive data-driven decision-making. A commitment to continuously searching for and implementing areas of improvement to enhance the customer experience is critical to the ISO 9001 standard.
6. Evidence-based Decision Making
In today's data-driven world, decisions must be grounded in empirical evidence rather than intuition alone. This principle relies on the benchmarking, collection and evaluation of data to support and inform all decision making—from equipment maintenance to delivery time. Evidence-based decision making allows executives to make informed decisions that can drive operational excellence and mitigate risks effectively.
7. Relationship Management
ISO 9001 recognizes the importance of relationships across the supply chain and the careful and consideration management of them as a key to success. From suppliers and vendors to customers and partners, this principle requires managers to go beyond transactional interactions, fostering strategic partnerships based on mutual trust and transparency in an effort to benefit all stakeholders involved.
When evaluating potential suppliers to add to the supply chain, a review of their certifications, in particular the ISO 9001 standard, is a key step in creating a competitive edge in the global marketplace. The Textile Business at Milliken has 23 manufacturing facilities in North America, Europe and Asia. A full list of Milliken Textile facilities with ISO 9001 certifications can be found online.