Six Sigma - a Renaissance or Rebalance
Six Sigma - a Renaissance or Rebalance?
作者 : Ian Gabrielides
An Introduction to Six Sigma
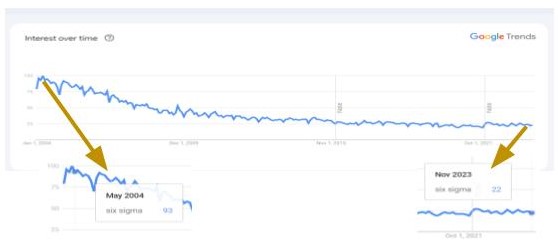
Lets start with explaining what Six Sigma is..
What is Six Sigma?
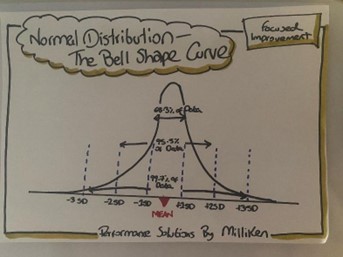
Six Sigma is a set of methods and tools for business process improvement that focuses on identifying and eliminating errors and/or defects. Six Sigma is a way of improving processes to increase the repeatability and accuracy of process results. The term Six Sigma originates from statistical analysis in quality control, a reference to the fraction of a normal ‘bell shaped’ curve that lies within six standard deviations of the mean, used to represent a defect rate. It’s widely accepted that Bill Smith, the US engineer introduced Sigma whilst working at Motorola in 1986.
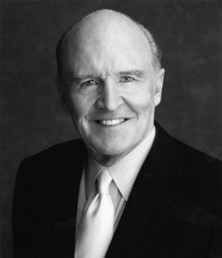
Other early adopters included General Electric (GE) 1995 and Honeywell 1998. Although exact numbers are difficult to obtain, it’s believed that Motorola can attribute over $20 billion in savings to their adoption of Six Sigma. GE’s Six Sigma implementation is likely to have delivered similar savings. Six Sigma was brought to the world’s attention by GE’s CEO Jack Welch who remains synonymous with Six Sigma today. Over the twenty-year period that Welch led GE their revenues grew from $26.8 billion to nearly $130 billion. Welch was recognized by Fortune Magazine in 1999 by being named ‘Manager of the Century’.
For some, Six Sigma is a natural statistics-led evolution from Deming’s Plan-Do-Check-Act (PDCA) problem solving methodology. Six Sigma projects deploy one of two 5 step disciplined problem solving methodologies
- DMAIC - Deployed when the objective is to improve a business process
- DMADV – Deployed when the objective is to build a new process or product
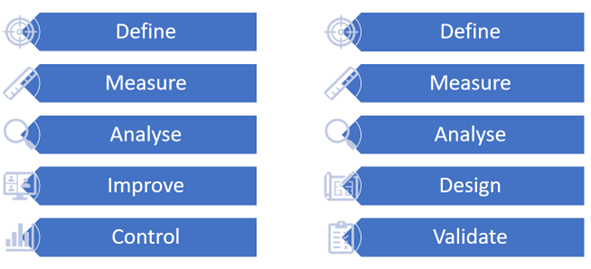
If your team is looking to improve your manufacturing processes, reduce costs, and improve efficiency, check out our manufacturing consulting services, including:
- Operational Excellence Consulting
- Manufacturing Safety Consulting
- Rapid Improvement Consulting
- Supply Chain Consulting
Why the Decrease in the Popularity of Six Sigma?
As mentioned earlier, online interest in 6 Sigma peaked in 2004 and searches steadily fell from this peak. A similar trend can be identified on LinkedIn over the same time frame, with fewer and fewer of its 630 million users adding Six Sigma as a skill to their profiles. So why the decrease in popularity?
The Great Belt Race
Some leaders may have misunderstood what Six Sigma is and how it can benefit their organisation. These misunderstandings led to some poor decision making; numerous businesses deployed a Six Sigma programme because they felt they should do, rather than identifying the opportunities that Six Sigma can address. This led to the great belt race, when the primary objective became the number of certified Six Sigma personnel rather than attacking losses. When an individual is certified to a level within the Six Sigma framework, they are awarded a coloured belt. To obtain a Six Sigma certification, individuals must pass a Six Sigma written test and deliver a project demonstrating the use of the Six Sigma toolbox. There are different belt colour/grade requirements for both the written test and the project delivery. Numerous people found themselves in a situation where they struggled to identify a true Six Sigma project to supplement the written part of their Six Sigma certification, and with pressure to achieve a target number of certified individuals, numerous projects were ‘shoehorned’ into the Six Sigma framework to get people ‘signed off’. This led to negative reflections when leaders reviewed their Six Sigma process.
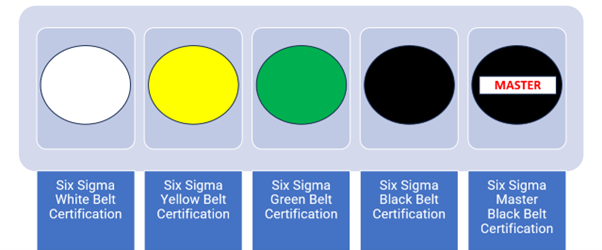
DMAIC Light and Lean
To achieve the belt certification many projects were being pushed into the Six Sigma project hopper. It became
quickly evident that Six Sigma was over detailed and complicated for some opportunities. This led many to question
their investment in their Six Sigma programme. Instead of understanding that lean Six Sigma is a tool, and like
all tools, it should be deployed, when necessary, some organisations cancelled their Six Sigma programmes.
One of the concerns with Six Sigma is the time it takes to complete a project. Many organisations were able to take the 5 step methodologies and follow a DMAIC light path and thus collapse the time taken to complete the project and deliver the result. Also, their Lean programmes were able to deliver most of the improvement objectives.
Decentralised 6 Sigma and Continuous Improvement Functions
The credit crisis of 2008 and the subsequent global slowdown had a big impact on many organisations. The need to tighten the financial belt led to a pause or a curtailment of many corporate CI teams and programmes. Numerous Six Sigma programmes fell victim to cuts where organisations prioritised quick short-term savings. As the recovery kicked in the appetite and desire to get Six Sigma training going again wasn’t what it was four or five years earlier.
Defect elimination fatigue
Some organisations reflected that they just got fatigued chasing defects. The Six Sigma goal of 3.4 defects per million opportunities is absolute; but this is not always an appropriate target. For some an unattainable target becomes a demotivator. For others they felt that they were witnessing diminishing returns, with smaller improvements and savings for the energy, effort, time, and money they invested in their Six Sigma programme.
Alternative Methodologies
The emergence of methodologies like Agile, Lean UX from the world of software development have surpassed Six Sigma in many organizations. The dynamism to get a solution out to the customer and refined over a period of sprints has been preferable to the rigorous focus on data required by Six Sigma. Six Sigma has been criticised for being too slow to deliver results to business and manufacturing processes in a world of changing market conditions where speed of execution is critical.
Shared Unpleasurable Six Sigma Experiences
The opportunity to communicate our experiences exploded with the exponential growth of social media and communication tools such as Skype, Zoom, Teams etc. In the mid-2000’s the onus was on the individual to seek Six Sigma reviews via a search engine. By the end of the decade and into the 2010’s shared 6 Sigma experiences would be at the palm of our hands, on social media via our smartphones. In the same period 6 Sigma pioneers GE and Motorola both experienced some turbulent times leading many to question the longer-term benefits of Six Sigma. Though both organizations still performed at high levels and much of the turbulence had no relationship with their Six Sigma programs.
Six Sigma is what we do, not something we do………
One of the reasons why Six Sigma may not be listed as a skill on a person’s LinkedIn profile or searched online as frequently is that it has become an established part of many organizations performance system which leads to us the final part of the question has has there been something of a Six Sigma revival – and why?
Six Sigma today
Has there been a 6 Sigma resurgence and why?
It’s difficult to say. Possibly there’s a new generation of people in Industry that are discovering Six Sigma for the first time. Many non-manufacturing organisations are experimenting with Six Sigma too. Industries such as healthcare, finance, hospitality, and logistics have recognized the value of Six Sigma. Maybe there is more of a maturer, more balanced use of Six Sigma now? The cornerstone of improving processes is a solid three to six-month project following the DMAIC steps; this will not change. However, demand for smaller “rapid improvement events” that deploy some 6 Sigma tools has become more popular. The idea of blended Lean Six Sigma methodology and process thinking has become an established component of daily operations. Not every process improvement effort needs to be a huge project. Making process improvement activity simple and accessible to everyone when deploying the correct Six Sigma tools has become a benefit to many businesses.
Suggesting a Six Sigma renaissance that reaches the popularity of the mid-00’s is perhaps fanciful but maybe there has been a realisation that organisations need Six Sigma capabilities to address opportunities in today’s fast-paced and ever-evolving business landscape. Organizations continue to seek ways to enhance operational efficiency, eliminate waste, and deliver superior customer value. One methodology that has proven its effectiveness over the years is Six Sigma. Combining Lean principles, which focus on waste reduction and process optimization, with Six Sigma's data-driven approach to minimizing defects.
The digital revolution
Globally, digital transformation continues to reshape industries, Six Sigma has embraced the integration of digital technologies to enhance its effectiveness. Today, organizations are leveraging advanced analytics, artificial intelligence (AI), and machine learning (ML) to complement Lean Six Sigma methodologies. These technologies enable faster and more accurate data analysis, leading to improved decision-making and proactive problem-solving. By harnessing the power of big data and predictive analytics, organizations can identify patterns, anticipate issues, and prevent defects before they occur.
IoT influence on Six Sigma.
Data collection: the requirement to obtain accurate actionable data through a robust operational definition is one of the challenges of the DMAIC ‘M’easure step. The advancement of technologies has significantly aided this activity. IoT, (the Internet of Things) has had a huge influence on this. What is IoT? The Internet of Things (IoT) describes the network of physical objects, ‘things’ that are embedded with sensors, software, and other technologies for the purpose of connecting and exchanging data with other devices and systems over the internet.
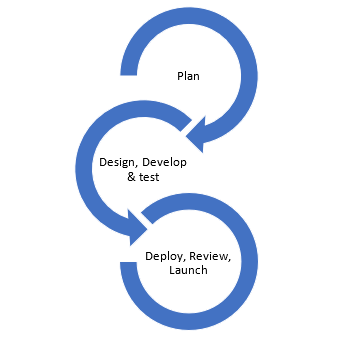
Customer/ User involvement in development.
Collaboration with other practices such as Agile has seen Six Sigma evolve. Organizations are incorporating customer feedback and sentiment analysis into their Lean Six Sigma initiatives to identify areas of improvement that directly impact customer satisfaction. By integrating customer feedback loops, organizations gain valuable insights to prioritize improvement efforts and enhance the overall customer experience.
In Conclusion
Darwin defined evolution as ‘descent with modification’, maybe it took a little longer for Six Sigma to evolve, or maybe Six Sigma required that digital spark to make it more relevant or more appealing again. But there is evidence that the use of Six Sigma has adapted in response to the changing environment. Its appeal now far out stretches the manufacturing arena where it was once only positioned. It’s unlikely to be the new shiny, must do initiative that it was when I first entered the manufacturing industry in the early 2000’s but it’s clearly found a place, a role in the digital age, and most importantly, it continues to deliver results.
If your team is looking to improve your manufacturing processes, reduce costs, and improve efficiency, check out our
manufacturing consulting services, including:
- Operational Excellence Consulting
- Manufacturing Safety Consulting
- Rapid Improvement Consulting
- Supply Chain Consulting